Water Treatment
of Hydraulic Fracturing Waste Water
Apr. 2013
I started my career on the R&D side of petroleum products - oils/lubricants, fuels, and ATF fluids prior to their finishing and certification. After much consolidation of the major oil companies in the late 1990s and early 2000s, I decided to change career paths and studied advanced water treatment, eventually moving into that industry in 2004. With the exception of a time in the energy sector producing high purity water through the use of IX, RO, and EDI, for use in both the steam cycle of power plants as well as auxiliary cooling, I've most recently been involved in the production of potable water through the use of reverse osmosis in support of our troops in Iraq, Kuwait, and Afghanistan under the USG LOGCAP program. Unfortunately the types and methods of water treatment available in the real world, has limitations that were frequently exceeded in an active warzone. KBR management had the foresight early on to create a basic water course or primer for this expeditionary field environment and I was fortunate to be selected to teach the course at the KBR Theatre Training Center in Baghdad as well as at sites throughout Iraq and Afghanistan.
I believe advanced water treatment together with recycling and reuse is the future for the majority of the water used in the hydraulic fracturing industry worldwide. I also believe it will be revolutionized by research and development through smaller specialist water treatment companies driven by the major players in the oil & gas industry (as well as governmental agencies through eventual regulation) in the United States. It is only a matter of time before advanced water treatment of the frac waste water stream, both the produced and flowback water is deemed an integral part of any operation, not only for economic reasons but almost as importantly, for environmental reasons.
One of the more controversial aspects of hydraulic fracturing is its dependence on large amounts of water, oftentimes in areas of the country already facing severe restrictions in water use. I believe in order for continued growth, the fracturing industry must adopt recycling and reuse practices or develop methods utilizing brackish or brine water in the frac fluids, and in turn they can use this opportunity in promoting their good stewardship of the environment.
There are many aspects in the treatment of fracturing waters that pose problems still in need of viable and cost effective solutions. Even though progress is steadily being made, and it will take an advancing, technologically driven solution with sound financial rewards to convince the major players ultimately, I can see no other way the industry can continue its growth at the pace at which it is currently growing without doing so. It is my goal to be a part of this emerging field and help those companies lead the way.
- James V. Delgado
Eagle Ford Shale
Apr. 2013
The Eagle Ford Shale is transforming San Antonio into an energy hub and the shale play's development has become a powerful economic engine for the city and all of South Texas.
Almost as desolate as Iraq & Afghanistan but at least there are no rockets or mortars raining down or VBIEDs driving into work! I'll take desolation over carnage any day of the week and be extremely grateful about it.
The Eagle Ford Shale is a 400-mile-long, deep formation of tight rock that sweeps from East Texas south below San Antonio to Mexico. Advances in technology have enabled drilling companies to extract much more oil and natural gas from tight shale rock.
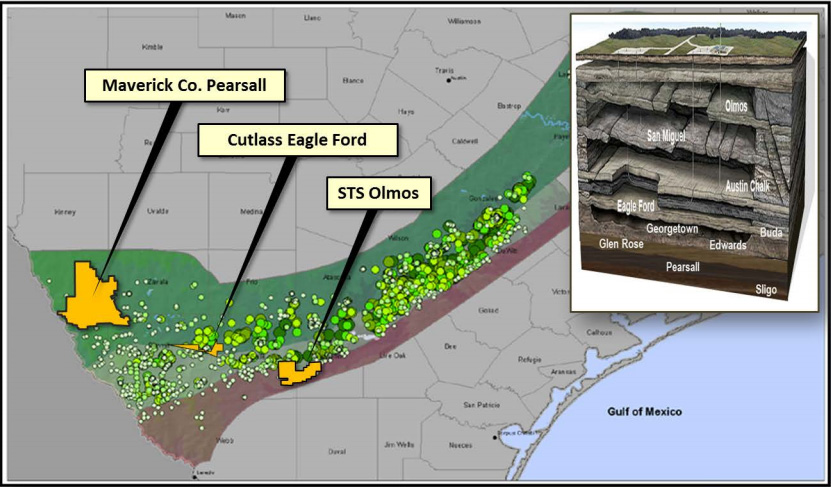
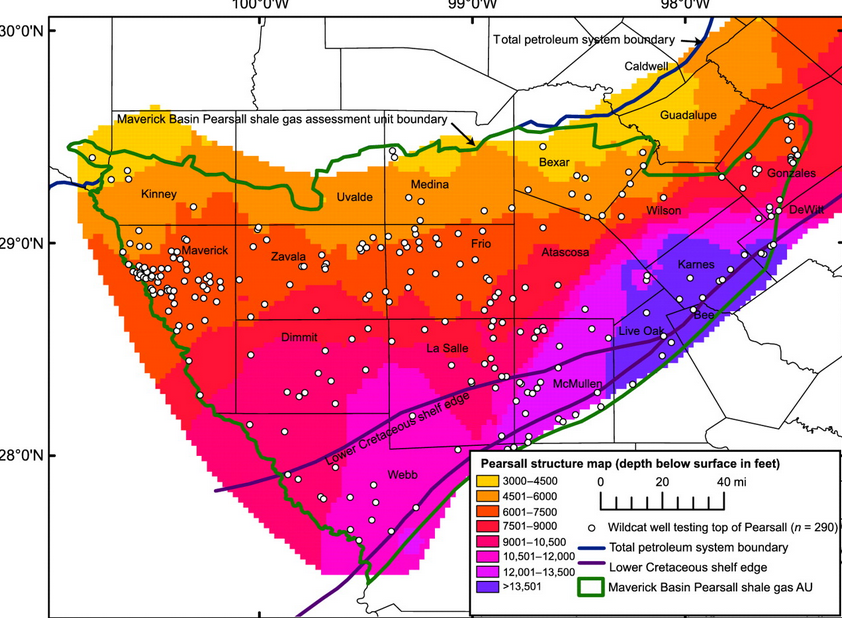
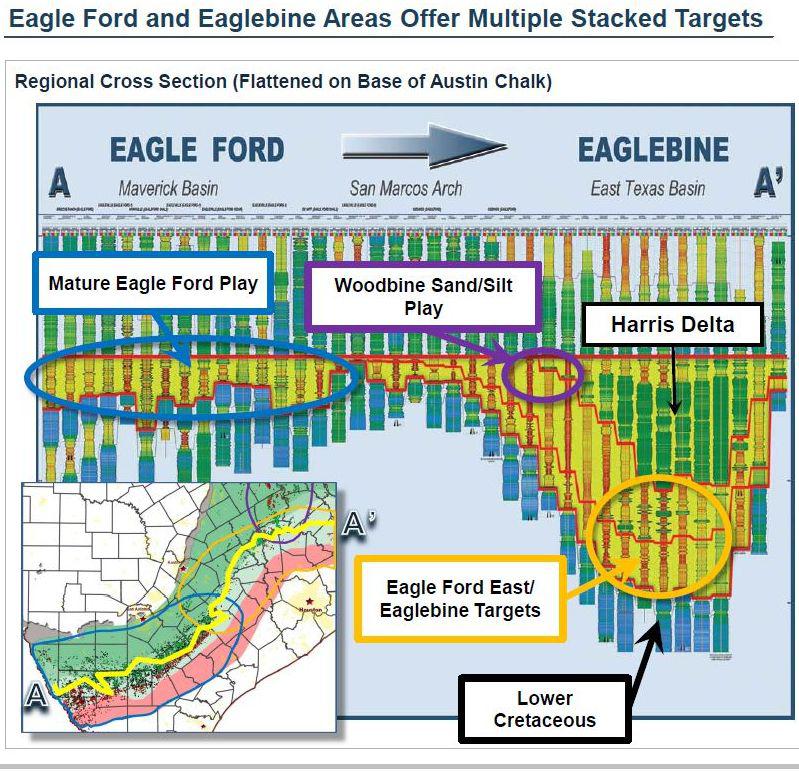
In late 2008, a successful well drilled by Houston-based Petrohawk Energy Corp. touched off the frenzy of leasing in the Eagle Ford Shale.
Railroad Commissioner David Porter has said that development of the Eagle Ford shale "has the potential to be the single most significant economic development in our state's history."
The vast oil and gas play in South Texas contributed $25 billion in total economic output to a 20-county South Texas region last year and provided 47,097 full-time jobs, according to a study prepared by the Center for Community and Business Research at the University of Texas at San Antonio's Institute for Economic Development.
SOURCE: San Antonio Express-News
Forward Osmosis
Jan. 2014
Now here is an innovative use of the osmosis process in the oil&gas industry - only it is not reverse osmosis, it is forward osmosis! Now this is what I am talking about! Basically what you have in forward osmosis is just the opposite of reverse osmosis. In reverse osmosis, you take a brine stream and under pressure, force the water molecules to permeate the semipermeable membrane and in the process produce a purified water stream. This is all well and good until you start seeing source waters with TDS ranging from well above seawater, 70,000 to 200,000. In reverse osmosis you must overcome the osmotic pressure through the use of a high pressure pump. As we all know, the osmotic pressure is a direct function of the amount of dissolved solids or TDS of the water; the higher the TDS, the higher the osmotic pressure. So your limiting factor in reverse osmosis (and why it is not an effective treatment alone in treating produced/flowback waters) is the over-all ability of your HPP to produce these extreme high pressures and your system and its components to withstand these extreme high pressures. By utilizing forward osmosis, you take this out of the equation because now instead of forcing the water molecules under high pressure through the membrane, you actually draw them through by use of a highly concentrated solution (much more concentrated than your feed stream). This in turn leaves the salts of the original solution behind in a highly concentrated brine solution with the water molecules now on the other side mixed in with the draw solution. Once that has happened, now you just need to separate them into two streams - a pure water solution and the draw solution which is reused in the process. Ingenious! This is the kind of technology that is being developed for use in the oil&gas industry right now and it is happening right here in Texas. Once perfected, I can see this process being utilized around the world as more countries jump (and they will) on the horizontal drilling and hydraulic fracturing bandwagon.
Here is the process explained graphically, much easier to understand than my convoluted explanation above!
The company is Oasys Water (great website by the way) out of Boston, Massachusetts and their process is called the Membrane Brine Concentrator or MBC4000
Here is an article about this process on Desalination.com
Fracking and the Drought in Texas
Feb. 2014
Hydraulic fracturing is competing for water in some of the driest regions of the U.S., including the Eagle Ford Shale in South Texas, according to a research paper released Wednesday by the nonprofit Ceres. The report said the Eagle Ford had the highest water use of any region in the country — 19.2 billion gallons — in an 18-month period and faces some of the biggest water challenges of any shale field in North America. South Texas operators used an average of 4.5 million gallons to fracture each well, the report states. It found that 98 percent of the Eagle Ford wells were in areas of medium or high water stress, with 28 percent in areas of high or extreme water stress. Dimmit County used about 4 billion gallons of water for fracturing — more than any county in the U.S. during the time period. Ceres also found that 70 percent of the wells in the Permian Basin in West Texas are in areas of extreme water stress — and water use in both that field and the Eagle Ford is expected to double in the next decade.
“This model cannot continue indefinitely,” said Monika Freyman, report author and senior manager in the Ceres water program. “The financial community needs to be aware of these potentially material risks.” Not only do companies and investors need to be concerned about water sourcing, but also whether operators can maintain enough goodwill in communities — the social license to operate, she said. The report calls for more creative water management, minimizing freshwater use and better long- term planning for the water infrastructure needed for oil and gas development — everything from the evaporation covers on water pits used by Pioneer Natural Resources to the use of brackish water aquifers and recycling.
“Water use for hydraulic fracturing can be a small percentage statewide — 1 or 2 percent,” Freyman said. But “the local use at the county level can be very large, sometimes equivalent to all the water use by all of the residents. It can be very stressful if you look at that scale.” Water always has been needed for oil and gas drilling, but not in this quantity.
Hydraulic fracturing pumps a mix of water and chemicals at high pressure to break the shale. Then sand is added to the fluid in increasing amounts to hold open the fissures, letting oil and gas flow up the well to the surface. Amanda Brock, CEO of Houston-based Water Standard, a water treatment firm, said that seven years ago, no one would have predicted the shale boom. “As a new user that wasn't anticipated in an already stressed system, how do we take real data and all come to the table to come up with a sustainable solution?” Brock asked. She called Texas “ground zero” because the Eagle Ford and Permian are two of the country's most productive fields, with more drilling expected. “If we keep on the growth curve we are on in the dry Eagle Ford, in 2015 it will be the largest stand- alone energy project in the world,” Brock said. Oil and gas companies have to get rid of water that returns after hydraulic fracturing, called flowback water, and the water that comes out the rock itself — production water.
While recycling and reuse are on the increase, often the wastewater gets trucked to disposal wells, where it's pumped underground far below freshwater aquifers. “Recycling is something we could advocate for,” Freyman said. “It's not the silver bullet.” Omar Garcia, president and CEO of the industry group South Texas Energy & Economic Roundtable, said some companies are reporting a decrease in their water use of as much as 30 percent, and that freshwater use in the Eagle Ford should drop with new technologies.
“Companies are continuously looking into technology to utilize more brackish water and aid in increasing water recycling, along with ways to decrease the amount of water used in our operations,” Garcia said. The Ceres report said recycling is complicated in the Eagle Ford region by the fact that the formation only returns a small percentage of water after hydraulic fracturing. Recycling is a more promising option in the Permian because of a high level of flowback water and a relatively low salinity level of the produced water, it said.
Steven Heim, managing director and director of environmental, social and corporate governance research and shareholder engagement at Boston Common Asset Management, said the industry is doing a lot of work to reduce the use of freshwater, but that it's hard to come by anything but anecdotal evidence. In the rapidly developing Eagle Ford, water use has already outpaced peak estimates.
SOURCE - San Antonio Express-News
Hydraulic Fracturing Giving Rise To New Water-Treatment Technologies
Here's information on emerging technologies that I've culled from just some of the players in frac water treatment:
This is an exciting time to work in the field of advanced water treatment in the oil & gas industry in the US and especially south Texas.